The machinist I spoke with used to do some work with Reliance Gear Corp. here outside Chicago, in Addison, IL. He's still friends with the owner of the outfit, and suggested speaking with them as well, they supposedly do excellent work. The manufacturing scene around Chicago is definitely not what it used to be, but is still going pretty strong, and I might try to get an operator / designer position at a fab shop or something for a year after I graduate until my girlfriend finishes up at Cambridge.
Walter Wong said I could work for him in L.A., and Dave Kennedy is still trying to move his operation over to Upstate NY where he's got his new property, and thought I might be able to help with fab stuff too. I'm going to apply to a rotational position at Lotus, and maybe Race Engineering grad program at Cranfield in the UK, or Chalmers in Sweden, and some mechanic / tech positions on mid level series race teams, like Formula BMW or Atlantics. Does anyone know the guys running that Canadian Touring Car 9-3SS?
I'd like to persue some solutions stateside for us though. We'd need to actually expend some money seeing if it's possible to REM or re-heat treat and cryo the gearsets, or if the sets are just too old and not up to it. A fair bit of time speaking with the old Swedes and anyone else who knows their way around the failures to get some hard data on the different failures and get real causes.
So definitely not a short term thing, but when I finish up here in the Spring I can put a fair bit of time back into this depending on what I'm doing.
I'll see what else I can find out in the mean time. I don't have my extra boxes here in IL though, they're back home in CA, and I won't be able to get many measurements or anything till I finish up.
On a related note, does anyone know the input to output shaft center-to-center distance if I was going to look into getting gearsets or new output shafts designed? The tooth profiles are dependent on the pitch circles and shaft center distances, the cutters are shaped specifically for the geometry of the assembly this is going in.
Best,
Drew
Strongest Gearbox Possible
- DrewP
- Posts: 2084
- Joined: Wed Dec 26, 2007 8:27 pm
- Nickname: TANK
- Number of Saabs currently owned: 1
- Location: Monrovia, CA
Re: Strongest Gearbox Possible
"You can educate ignorance, but you can't fix stupid."
Re: Strongest Gearbox Possible
Here is a pic of the output shaft from my rebuild
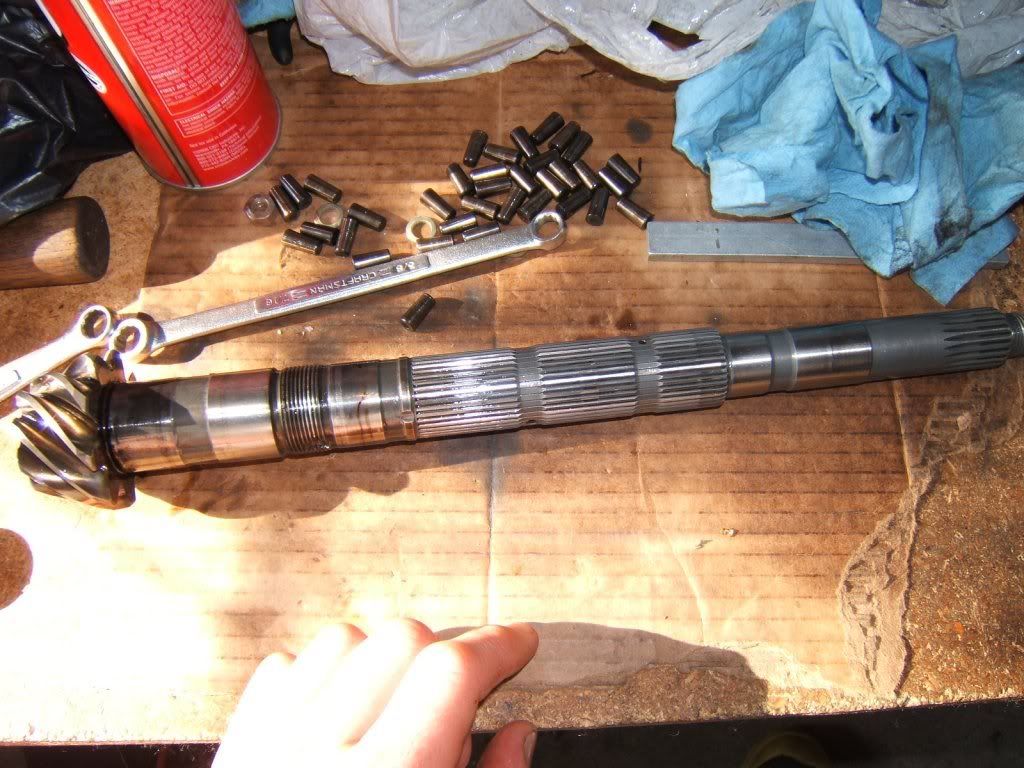
I'm no material engineer (I have to read your posts twice to understand them Drew) but I have a hard time seeing this thing flexing.
I do agree with you that the primary case is quite beefy. It weighs as much as the main case.
Now,
I'm finishing up a BS degree in metal casting. I have an '89 box that I'm going to tear down this spring and hope to get scanned by a laser CMM to give me an accurate 3d model. From there, I plan to develop a suitable casting design for the main case to be cast from ductile iron.
I make no promises about the completion of this project nor do I believe this will be a cure for the c900 plague. However, solutions to this problem need to be developed and pursued on this side of the pond.
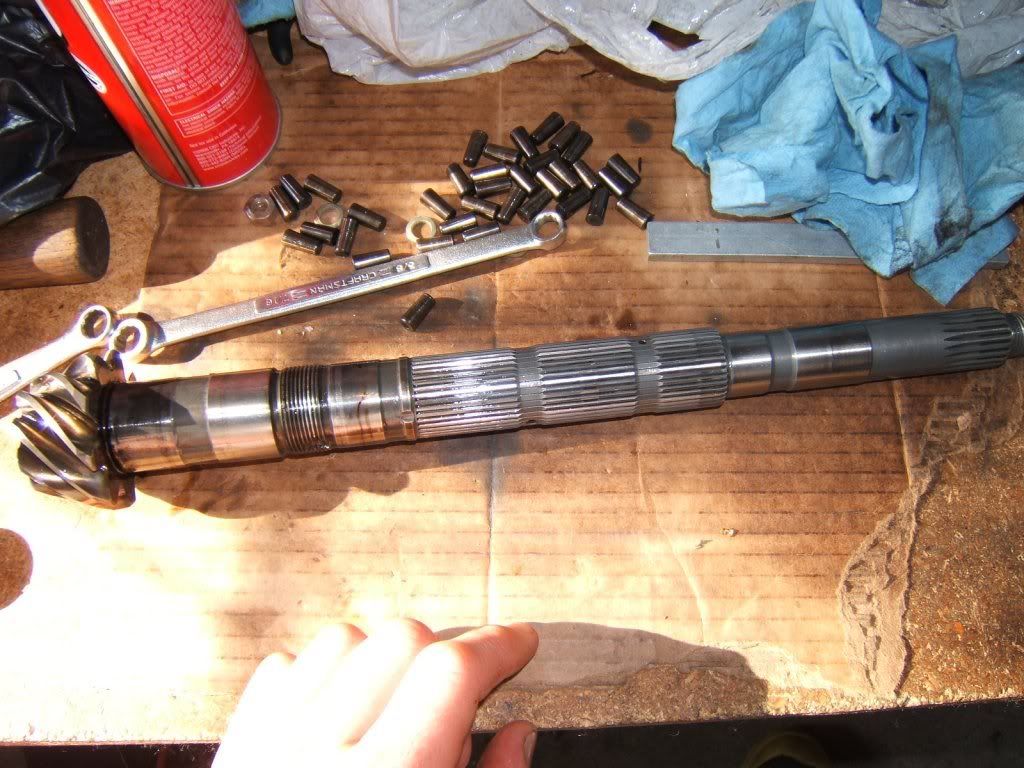
I'm no material engineer (I have to read your posts twice to understand them Drew) but I have a hard time seeing this thing flexing.
I do agree with you that the primary case is quite beefy. It weighs as much as the main case.
Now,
I'm finishing up a BS degree in metal casting. I have an '89 box that I'm going to tear down this spring and hope to get scanned by a laser CMM to give me an accurate 3d model. From there, I plan to develop a suitable casting design for the main case to be cast from ductile iron.
I make no promises about the completion of this project nor do I believe this will be a cure for the c900 plague. However, solutions to this problem need to be developed and pursued on this side of the pond.
- DrewP
- Posts: 2084
- Joined: Wed Dec 26, 2007 8:27 pm
- Nickname: TANK
- Number of Saabs currently owned: 1
- Location: Monrovia, CA
Re: Strongest Gearbox Possible
I remember when this idea came up on the Link forum like last summer? I'm glad to see you're still persuing the project, it will be interesting to follow, and I give you credit, the factory castings are extremely complicated and duplicating something suitable will be no easy feat to get the amount of finish machining down to an acceptable level.
I'm not sure how it came across, I will have to re-read what exactly I posted about the shafts, but what I was trying to say was that on a stiffness basis, that splined output shaft should be much much less bending rigidity than the input cluster and the bearing retaining areas in the two bulkheads, and if the shafts flexing really is causing measureable misalignment the first thing I would do to address it would be do something about either supporting the middle of that shaft to the upper left corner of the case, or support the two shafts to each other, and then see where that gets you.
If 80% of the deflection is happening in the shafts and 20% in the bulkheads, then the new case won't help much. Just because the case is aluminum doesn't automatically mean it has low rigidity. Rigidity has much more to do with geometry than materials properties, and steel alloys and aluminum alloys have very close to the same stiffness to weight ratio.
The fact that the output shaft has the splines and oiling holes and varying diameters cut into it lessens the rigidity even more.
Even if you are able to get a good scan of the original and keep all the dimensions the same I expect most of your time will be spend adjusting section thickness to keep the cooling rates reasonable so that the thing doesn't come out so warped as to be unuseable, since the original geometry was designed around the heat transfer coeffs of the AL.
Are you still thinking sand cores? Or machineable foam ones, or something else like that?
Best,
Drew
I'm not sure how it came across, I will have to re-read what exactly I posted about the shafts, but what I was trying to say was that on a stiffness basis, that splined output shaft should be much much less bending rigidity than the input cluster and the bearing retaining areas in the two bulkheads, and if the shafts flexing really is causing measureable misalignment the first thing I would do to address it would be do something about either supporting the middle of that shaft to the upper left corner of the case, or support the two shafts to each other, and then see where that gets you.
If 80% of the deflection is happening in the shafts and 20% in the bulkheads, then the new case won't help much. Just because the case is aluminum doesn't automatically mean it has low rigidity. Rigidity has much more to do with geometry than materials properties, and steel alloys and aluminum alloys have very close to the same stiffness to weight ratio.
The fact that the output shaft has the splines and oiling holes and varying diameters cut into it lessens the rigidity even more.
Even if you are able to get a good scan of the original and keep all the dimensions the same I expect most of your time will be spend adjusting section thickness to keep the cooling rates reasonable so that the thing doesn't come out so warped as to be unuseable, since the original geometry was designed around the heat transfer coeffs of the AL.
Are you still thinking sand cores? Or machineable foam ones, or something else like that?
Best,
Drew
"You can educate ignorance, but you can't fix stupid."
- Crazyswede
- Team Turbo Troll Crew
- Posts: 4540
- Joined: Fri Sep 22, 2006 3:53 pm
- Nickname: Mongo
- Number of Saabs currently owned: 97
- Location: Vermont
- Contact:
Re: Strongest Gearbox Possible
put 300 to 400 lbs of torque into it when the wheels are not turning and all kinds of things will happen that you cannot imagine including: shaft flex, deflection, case deformation, bearing failure etc etc. If you know the alloy of the shaft you could do some simple calculation based on how it is loaded to determine what load you can expect to see a problem at.
I don't have my old notes or texts in front of me to remember these calculations at the moment. My time over the last 5 years has focused on hot forging of turbine blades for GE aircraft engines.
I don't have my old notes or texts in front of me to remember these calculations at the moment. My time over the last 5 years has focused on hot forging of turbine blades for GE aircraft engines.
I am the 73%
Re: Strongest Gearbox Possible
Yeah, this idea came up on the link several years ago. Same idea, but a different person pursuing it. I post under "Nate" there too. I've had this dream ever since I declared this major.
The molding will be done with sand. I have not decided on the binder system for the sand. I'm leaning towards using a phenolic urethane no-bake binder system (chemically cured). This will allow me to make molds without using flasks (metal "picture" frame holders) or specialized molding machines.
I don't think redesigning the case to be made out of iron rather than aluminum would be that difficult. An iron case would need to be thicker along the outside walls, otherwise it may form white iron due to the rapid cooling of the thin sections. Are those horizontal ribs necessary or could I just fill them in?
The challenge for me is to design the pattern. In order to produce the inside cavity, multiple cores are going to have to be used. They will have to be quite large and long, so that will be quite fun supporting all of that sand from one end.
Plus the case is quite long so there may be trouble making the iron flow through thin long sections. One thing at a time though.
The molding will be done with sand. I have not decided on the binder system for the sand. I'm leaning towards using a phenolic urethane no-bake binder system (chemically cured). This will allow me to make molds without using flasks (metal "picture" frame holders) or specialized molding machines.
I don't think redesigning the case to be made out of iron rather than aluminum would be that difficult. An iron case would need to be thicker along the outside walls, otherwise it may form white iron due to the rapid cooling of the thin sections. Are those horizontal ribs necessary or could I just fill them in?
The challenge for me is to design the pattern. In order to produce the inside cavity, multiple cores are going to have to be used. They will have to be quite large and long, so that will be quite fun supporting all of that sand from one end.
Plus the case is quite long so there may be trouble making the iron flow through thin long sections. One thing at a time though.
- Crazyswede
- Team Turbo Troll Crew
- Posts: 4540
- Joined: Fri Sep 22, 2006 3:53 pm
- Nickname: Mongo
- Number of Saabs currently owned: 97
- Location: Vermont
- Contact:
Re: Strongest Gearbox Possible
you better cast up at least 5 of the cases that way you won't feel so bad when you destroy the only one you ever built.
of course I like a lot of others on here....as much as we like/love Saabs its still just a Saab. meaning that no matter how much you invest in the car its still a quirky low value machine...so you better be in it out of pure love etc. Airsweden and I have this conversation pretty regularly.
of course I like a lot of others on here....as much as we like/love Saabs its still just a Saab. meaning that no matter how much you invest in the car its still a quirky low value machine...so you better be in it out of pure love etc. Airsweden and I have this conversation pretty regularly.
I am the 73%
- Geoff
- Team Turbo Troll Crew
- Posts: 3890
- Joined: Fri Oct 20, 2006 3:31 pm
- Nickname: Geoff
- Number of Saabs currently owned: 6
- Location: Nude Humpshire
Re: Strongest Gearbox Possible
Then you need to keep in mind the extra weight of a cast iron gearbox. The front end of these cars can't take any more weight and be expected to handle well.
Cast iron is about 2.6 times heavier than cast aluminum. If the stock aluminum casting weighs about 40 lb then the cast iron would weigh 100 lb. Assuming you'd need to add 20% more material to make the iron flow you're up to 125 lb. Fortunately the weight is low.
I'd still try one out for the sake of it.
Cast iron is about 2.6 times heavier than cast aluminum. If the stock aluminum casting weighs about 40 lb then the cast iron would weigh 100 lb. Assuming you'd need to add 20% more material to make the iron flow you're up to 125 lb. Fortunately the weight is low.
I'd still try one out for the sake of it.
The kind of dirty that doesn't wash off 

- DrewP
- Posts: 2084
- Joined: Wed Dec 26, 2007 8:27 pm
- Nickname: TANK
- Number of Saabs currently owned: 1
- Location: Monrovia, CA
Re: Strongest Gearbox Possible
The weight is a bit of an issue I had in the back of my mind since the trans is so far forward, but when I had my last one apart I didn't weigh it but the primary case with everything removed I think only weighs about 15lbs, it's actually not that heavy. Definitely not more than 25lbs, so you might almost offset the increase just by moving the battery as far back as possible. Plus you guys still have moulds for the kevlar-glass hoods right?
What did just occur to me though was how important it would be to get all the passive oil circulation passages back in as close to stock as possible, and hopefully be able to use the factory scrapers built into the front output bearing retainer and those sorts of things, a ton of factory development time went into those and they work pretty darn well (I have never had trans problems from the oil all draining to the trans when climbing 7000ft mountain grades).
What about doing the case as a fabrication with bolt-connection bulkhead plates and bolt-on rear diff box instead of trying to do it all in one piece? It'd be easier to get all the locating bores in and modify the geometry until it works right, but definitely wouldn't be as rigid as a single cast piece. It could be as simple as an assembly of reinforced plate stock.
Neil, what do you think about doing an assembly?
Nate, another idea, what's the size / volume / path length limit for an investment casting? Would it be easier to have some members donate machine time to get a mould made to produce the wax patterns and produce them that way? Or is this going to be too big?
I exactly agree with you, that was where my comment that we need to compile notes from all the old-timers on the various failures, or try to instrument some hard testing on a complete box. I have had thoughts of getting a complete box, locking the tripod outputs, and loading the input sprocket with a long lever and something really heavy so that I could get in with a dial indicator and try to measure some of the misalignment and case deflection. Getting it tied down sufficiently would be the hard part. We have a big (4'x6' ?) cast iron welding table at school, but short of a chassis plate or an extra engine block to bolt to it'd be hard to fixture. I'd like to try to see actual numbers.
Those would be an estimate though, since when it's actually loading the shaft is rotating and almost certainly carries different loads depending on where everything is in the mesh and with temperature and things like that.
The last thing is that you don't actually have to know the alloy and specific properties to do deflection calculations, you need it for strength calculations. For shaft deflection analysis all you need is the Young's modulus, and it's basically the same for all the steel alloys.
Best,
Drew
What did just occur to me though was how important it would be to get all the passive oil circulation passages back in as close to stock as possible, and hopefully be able to use the factory scrapers built into the front output bearing retainer and those sorts of things, a ton of factory development time went into those and they work pretty darn well (I have never had trans problems from the oil all draining to the trans when climbing 7000ft mountain grades).
What about doing the case as a fabrication with bolt-connection bulkhead plates and bolt-on rear diff box instead of trying to do it all in one piece? It'd be easier to get all the locating bores in and modify the geometry until it works right, but definitely wouldn't be as rigid as a single cast piece. It could be as simple as an assembly of reinforced plate stock.
Neil, what do you think about doing an assembly?
Nate, another idea, what's the size / volume / path length limit for an investment casting? Would it be easier to have some members donate machine time to get a mould made to produce the wax patterns and produce them that way? Or is this going to be too big?
Crazyswede wrote:put 300 to 400 lbs of torque into it when the wheels are not turning and all kinds of things will happen that you cannot imagine including: shaft flex, deflection, case deformation, bearing failure etc etc. If you know the alloy of the shaft you could do some simple calculation based on how it is loaded to determine what load you can expect to see a problem at.
I exactly agree with you, that was where my comment that we need to compile notes from all the old-timers on the various failures, or try to instrument some hard testing on a complete box. I have had thoughts of getting a complete box, locking the tripod outputs, and loading the input sprocket with a long lever and something really heavy so that I could get in with a dial indicator and try to measure some of the misalignment and case deflection. Getting it tied down sufficiently would be the hard part. We have a big (4'x6' ?) cast iron welding table at school, but short of a chassis plate or an extra engine block to bolt to it'd be hard to fixture. I'd like to try to see actual numbers.
Those would be an estimate though, since when it's actually loading the shaft is rotating and almost certainly carries different loads depending on where everything is in the mesh and with temperature and things like that.
The last thing is that you don't actually have to know the alloy and specific properties to do deflection calculations, you need it for strength calculations. For shaft deflection analysis all you need is the Young's modulus, and it's basically the same for all the steel alloys.
Best,
Drew
"You can educate ignorance, but you can't fix stupid."
Re: Strongest Gearbox Possible
Just a Saab, bah! Just the best car ever built. There is no logical explanation for my love of c900's. I'm not pursuing this for any $$$, just for the love of the c900 and a chance to apply my knowledge. Plus, the c900 owners that frequent the forums aren't loaded with dough. Maybe they will come out of the wood work?
I took my empty main case to the car wash to power wash it when I did my rebuild. I was quite surprised about how little it weighs, maybe 10-15 lbs.
An investment casting is a possibility, it has been in the back of my mind. Still, the casting would need several large cores, unless someone were to machine a one piece wax pattern from a billet of wax.
An investment casting would reduce machining time, though I would still leave plenty of material around the driver bores and pinion housing bore for machining since their locations and dimensions are so critical.
I took my empty main case to the car wash to power wash it when I did my rebuild. I was quite surprised about how little it weighs, maybe 10-15 lbs.
An investment casting is a possibility, it has been in the back of my mind. Still, the casting would need several large cores, unless someone were to machine a one piece wax pattern from a billet of wax.
An investment casting would reduce machining time, though I would still leave plenty of material around the driver bores and pinion housing bore for machining since their locations and dimensions are so critical.
- DrewP
- Posts: 2084
- Joined: Wed Dec 26, 2007 8:27 pm
- Nickname: TANK
- Number of Saabs currently owned: 1
- Location: Monrovia, CA
Re: Strongest Gearbox Possible
Do you know what investment casting wax costs? If it's anything like the machineable waxes or foams for making machineable cores for composites layups it won't be cheap! The ability to gather all the chips back up and re-use it is definitely attractive though, but I have no idea what it costs. Is it just a parrafin?
Then you can just pack sand around the form? What refractory materials do you have to use around the wax? (My exposure to casting was almost exclusively with sand castings, have to pull my manufacturing book back out!)
I agree the hardest part will be to get the mold assembly with the necessary cores put together and getting everything to release correctly.
Wax cores transfer better dimensional accuracy, right?
Best,
Drew
Then you can just pack sand around the form? What refractory materials do you have to use around the wax? (My exposure to casting was almost exclusively with sand castings, have to pull my manufacturing book back out!)
I agree the hardest part will be to get the mold assembly with the necessary cores put together and getting everything to release correctly.
Wax cores transfer better dimensional accuracy, right?
Best,
Drew
"You can educate ignorance, but you can't fix stupid."
- Crazyswede
- Team Turbo Troll Crew
- Posts: 4540
- Joined: Fri Sep 22, 2006 3:53 pm
- Nickname: Mongo
- Number of Saabs currently owned: 97
- Location: Vermont
- Contact:
Re: Strongest Gearbox Possible
DrewP wrote:
The last thing is that you don't actually have to know the alloy and specific properties to do deflection calculations, you need it for strength calculations. For shaft deflection analysis all you need is the Young's modulus, and it's basically the same for all the steel alloys.
Best,
Drew
quite right...I was thinking about the alloy in terms of yield strength.
I am the 73%
- DrewP
- Posts: 2084
- Joined: Wed Dec 26, 2007 8:27 pm
- Nickname: TANK
- Number of Saabs currently owned: 1
- Location: Monrovia, CA
Re: Strongest Gearbox Possible
Sorry, must have got myself mixed up in what you were saying.
Has anyone broken the output shafts, or do the teeth always let go first?
Because there are probably things that could be done to those too. There is actually a materials lab on campus that can do an alloy decomposition on a sample to get you all the alloying elements and impurities so that you'd know how to go about developing a heat treat process for it if someone wanted to try to 'de-fatigue' the gearsets with an anneal, re-temper, maybe cryo and shot peen, which is what I'd probably do if I could find a good set of used gears with no surface pitting or abrasion failure on the flanks of the teeth (they gotta be nice and smooth!) that I wanted to use in a race box buildup. Start them fresh at the beginning of their fatique lives!
Are you guys hot forging nickel alloy turbine blades, or do you use something else? Do they start as single-crystal blanks, or castings?
Best,
Drew
Has anyone broken the output shafts, or do the teeth always let go first?
Because there are probably things that could be done to those too. There is actually a materials lab on campus that can do an alloy decomposition on a sample to get you all the alloying elements and impurities so that you'd know how to go about developing a heat treat process for it if someone wanted to try to 'de-fatigue' the gearsets with an anneal, re-temper, maybe cryo and shot peen, which is what I'd probably do if I could find a good set of used gears with no surface pitting or abrasion failure on the flanks of the teeth (they gotta be nice and smooth!) that I wanted to use in a race box buildup. Start them fresh at the beginning of their fatique lives!
Are you guys hot forging nickel alloy turbine blades, or do you use something else? Do they start as single-crystal blanks, or castings?
Best,
Drew
"You can educate ignorance, but you can't fix stupid."
- Crazyswede
- Team Turbo Troll Crew
- Posts: 4540
- Joined: Fri Sep 22, 2006 3:53 pm
- Nickname: Mongo
- Number of Saabs currently owned: 97
- Location: Vermont
- Contact:
Re: Strongest Gearbox Possible
we do all sorts of stuff titanium, aluminum, copper, stainless steel, nickel based alloys. Most of our stock comes as round stock and we cut it into slugs. A few processes use castings but I am not at liberty to discuss anything specific. We do our own heat treating, annealing, shot peening, REM'ing, tumbling, etc etc. basically all the processes needed to go from raw stock to ready for use in an engine. forging, gathering, extruding, upsetting.......and on and on.
I am the 73%
- 99Super
- Posts: 1065
- Joined: Wed Jan 24, 2007 5:14 pm
- Number of Saabs currently owned: 13
- Location: Bend, OR
- Contact:
Re: Strongest Gearbox Possible
As long as it's being proposed to cast an entire new gearbox, perhaps even having a separate diff box, why not jut design a box casting that will accept standard race gears?
Then the casting just has to fit the basic dimensions of the Saab engine base and maybe the front transfer chain housing and do what you want to the rest.
Personally, I always thought the 99/900 engine was in backwards (we all know it is) and the wheels should be at the front to eliminate the stupid overhang and forward weight bias.
It should be like the original Sonett...
Then the casting just has to fit the basic dimensions of the Saab engine base and maybe the front transfer chain housing and do what you want to the rest.
Personally, I always thought the 99/900 engine was in backwards (we all know it is) and the wheels should be at the front to eliminate the stupid overhang and forward weight bias.
It should be like the original Sonett...
_______________________________________________
"I don't want no Commies in my car!... No Christians either!"
"I don't want no Commies in my car!... No Christians either!"
- Crazyswede
- Team Turbo Troll Crew
- Posts: 4540
- Joined: Fri Sep 22, 2006 3:53 pm
- Nickname: Mongo
- Number of Saabs currently owned: 97
- Location: Vermont
- Contact:
Re: Strongest Gearbox Possible
though the current design is quite good at keeping the weight over the wheels....making them the good snow cars they are
I am the 73%
Return to “SAAB MOTORSPORT TECH”
Who is online
Users browsing this forum: No registered users and 12 guests